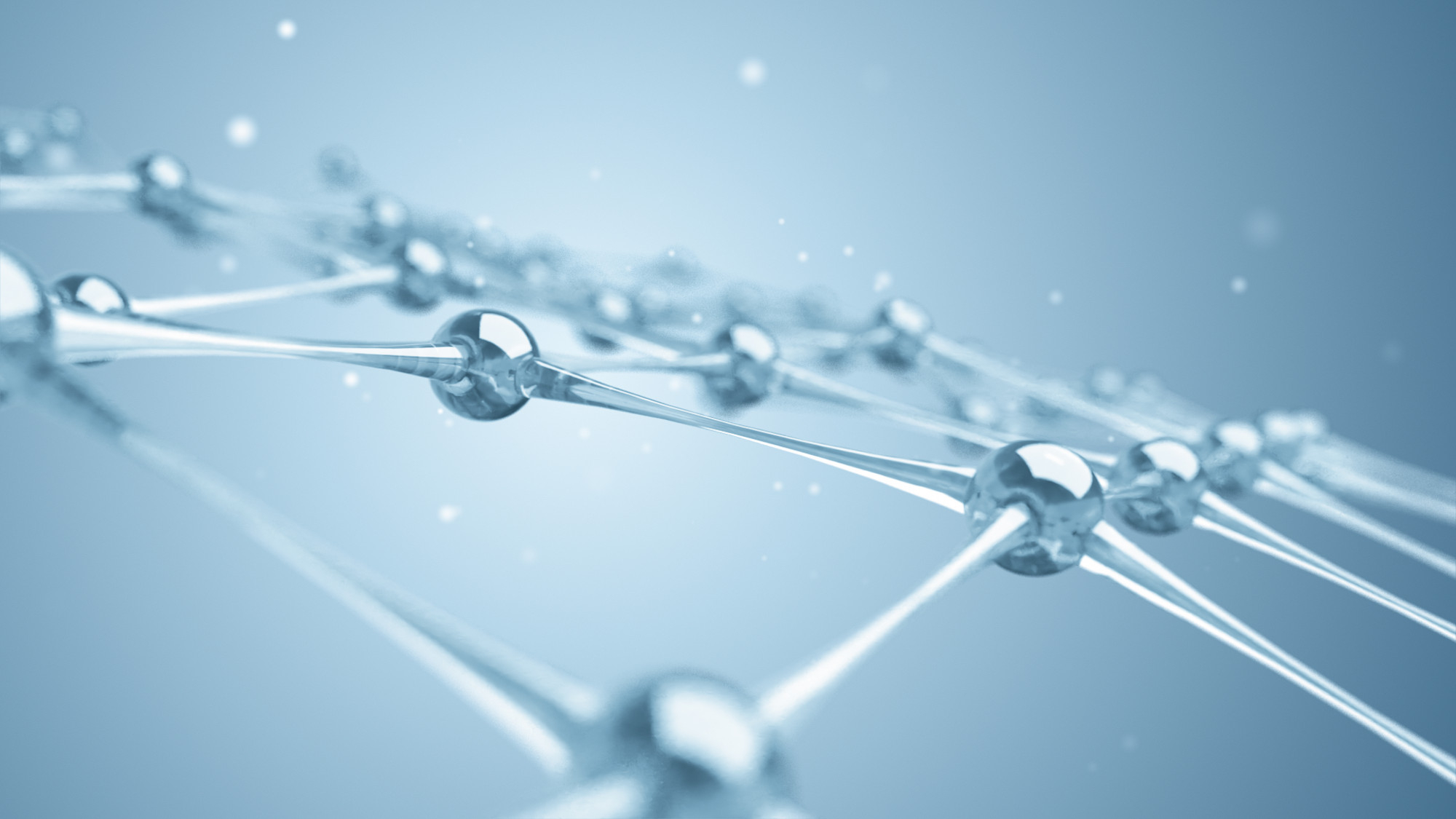
Il vetro è un materiale meccanicamente omogeneo e isotropo, con comportamento elastico-lineare fino a rottura, sia in trazione sia a compressione.
La resistenza meccanica del vetro a compressione è dell’ordine di 1000 N/mm2 ed è, in genere, molto maggiore della resistenza meccanica a trazione. Per tale motivo, in genere, la resistenza a trazione del vetro è la proprietà meccanica determinante nella progettazione.
In generale, col termine generico vetro si fa riferimento al vetro di silicato sodo-calcico float secondo EN 572-9.
VETRO FLOAT
Il vetro float rappresenta il vetro piatto più prodotto nel mondo, con circa il 90% di produzione globale. Esso è fabbricato con il processo di produzione messo a punto da Sir Alastair Pilkington nel 1952, in cui il vetro fuso è versato in un bagno di stagno ad atmosfera controllata. In tale condizione, il vetro galleggia sullo stagno, si distribuisce e forma una lastra uniforme. I differenti spessori sono ottenuti variando la velocità di estrazione del vetro dal bagno. Infine, un processo di raffreddamento controllato, detto ricottura, consente di ottenere il vetro finito perfettamente trasparente e con superfici parallele. Il processo produttivo consente di realizzare lastre di dimensioni massime pari a 6,00 x 3,21 m con taglio dei bordi longitudinali.
Il termine corretto per tale tipologia di vetro è “ricotto”, termine dovuto al suo processo di raffreddamento finale, ma molto spesso è anche semplicemente chiamato vetro “float”.
Gli spessori con cui vengono prodotte industrialmente le lastre di vetro sono i seguenti: 2 mm, 3 mm, 4 mm, 5 mm, 6 mm, 8 mm, 10 mm, 12 mm, 15 mm, 19 mm.
La resistenza caratteristica del vetro float è stata definita mediante uno studio sperimentale del gruppo di lavoro CEN/TC129-WG8 in cui sono stati sottoposti a prova 30 campioni portati a rottura, composti ciascuno da 25 provini quadrati di lato 1000 mm e spessore nominale 6 mm.
I risultati della prova sono stati molto dispersi, soprattutto per quanto riguarda i valori della probabilità di frattura inferiori al 10%.
Tarando la miglior curva di Weibull sui dati sperimentali ottenuti, si vede che il frattile inferiore al 5% associato i parametri statistici della distribuzione risulta pari a 45 MPa.
In definitiva, il valore minimo della resistenza caratteristica a trazione per flessione fg;k delle lastre di vetro ricotto da adottare per le verifiche di resistenza è pari a 45 MPa.
VETRO TEMPERATO
Il vetro temperato (thermally toughened glass) è ottenuto mediante un processo controllato di riscaldamento e raffreddamento per conferirgli una maggiore resistenza alle sollecitazioni meccaniche e termiche e caratteristiche di rottura prescritte. In tale tipo di processo, il vetro float è posto su rulli e viene fatto scorrere in un forno riscaldato alla temperatura di tempra di 640 °C. Una volta estratto dal forno, il vetro viene raffreddato velocemente con aria in movimento alla temperatura ambiente. In tal modo, la superficie esterna raggiunge subito la sua forma permanente, mentre la parte interna deve ancora raffreddarsi. Pertanto, il tentativo di restringimento della parte interna, ancora in fase di raffreddamento, genera uno stato di compressione nella superficie esterna. Tale compressione comporta che le fratture in superficie si possano aprire solo dopo aver esaurito le risorse di resistenza dovute allo stato di compressione esterna e solo allora potrà nascere uno stato di trazione nel vetro.
Pertanto, risulta chiaro che il vetro temperato sia decisamente più resistente del vetro float, in quanto il processo termico fa nascere delle tensioni meccaniche che tendono a chiudere i difetti superficiali.
Il valore minimo della resistenza caratteristica a trazione per flessione fb;k delle lastre di vetro presollecitato temperato termicamente da adottare per le verifiche di resistenza è pari a 120 MPa, ben maggiore di quello del vetro ricotto float pari a 45 MPa.
Inoltre, il processo di tempera influisce anche sul modo di fratturarsi del vetro, in quanto la grande quantità di energia che si accumula all’interno della lastra temperata comporta la rottura del vetro in frammenti di piccole dimensioni e con bordi non taglienti tali da non provare danni a persone o cose a contatto. Proprio perché gli spigoli dei frammenti sono smussati, questo tipo di vetro è detto di sicurezza
I vetri temperati vengono prodotti con spessori fino a 19 mm, in casi particolari possono raggiungere anche 25 mm di spessore.
Un particolare fenomeno che si può generare nel vetro temperato è la rottura spontanea dovuta alla presenza di inclusioni di solfuro di Nichel, anche molto tempo dopo la sua installazione.
Durante la produzione del vetro, nella massa fusa sono presenti particelle di nichel e di zolfo, in quanto componenti naturali delle materie prime del vetro. Durante il raffreddamento del vetro si formano dei cristalli di solfuro di Nichel (NiS) di minuscole dimensioni che in genere risultano completamente innocue nei vetri ricotti. Tali particelle posso trovarsi in due forme di cristallizzazione “Alpha” e “Beta”, caratterizzate da dimensioni differenti. Il passaggio di stato tra le due forme comporta un aumento di volume di circa il 4%, che in un vetro temperato infrangerebbe immediatamente la lastra, già soggetto ad elevate sollecitazioni di trazione dovute alla tempera.
La rottura che avviene per inclusione di particelle di solfuro di Nichel viene detta a “farfalla”, per la forme che assumono i cristalli rotti.
Al fine di prevenire la potenziale rottura spontanea, i vetri temperati vengono generalmente sottoposti ad un processo denominato HST (Heat Soak Test). In questa prova, le lastre vengono riscaldate ad una temperatura media di circa 290 °C per alcune ora. In tale condizione, l’alta temperatura a cui si trova il vetro favorisce la transizione tra le due fasi ed il conseguente cambio di volume delle particelle di solfuro di Nichel. Se la lastra rimane integra, è garantita l’assenza di inclusioni di NiS ed è possibile impiegarla.
Purtroppo, anche tale prova non è in grado di garantire al 100% l’assenza di inclusioni di solfuro di Nichel, ma ne riduce, ad ogni modo, notevolmente la probabilità di rottura spontanea del vetro.
Per tale motivo, è consigliabile far eseguire un trattamento HST per vetri temperati impiegati in pannelli di facciata, lastre fissate con vincoli puntuali tipo rotules, lastre di difficile sostituzione.
VETRO INDURITO
Il vetro indurito è ottenuto mediante un trattamento tale da indurre lungo lo spessore del materiale un campo di tensioni (trazione nello spessore e compressione sulla superficie) che permettono di inibire la propagazione delle fessure superficiali, aumentando così la resistenza meccanica e alle sollecitazioni termiche della lastra. In caso di rottura il vetro indurito si rompe in modo simile al vetro ricotto.
Il trattamento di indurimento può essere di tipo termico o chimico.
Il vetro indurito termicamente (heat strengthened glass) è ottenuto mediante un processo controllato di riscaldamento e raffreddamento simile a quello del vetro temperato, ma raggiungendo dei picchi di sollecitazione inferiori. Le caratteristiche (dimensionali, di frammentazione, di resistenza meccanica) minime sono definite nella norma di prodotto UNI EN 1863-1.
Essendo il valore di precompressione del vetro indurito termicamente inferiore a quello del vetro temperato termicamente, la resistenza caratteristica minima diviene circa la metà di quello completamente temprato ma resta comunque circa il doppio del vetro ricotto.
Il valore minimo della resistenza caratteristica a trazione per flessione fb;k delle lastre di vetro presollecitato indurito termicamente da adottare per le verifiche di resistenza è pari a 70 MPa.
Il vetro indurito chimicamente (chemically strengthened glass) è ottenuto sottoponendo un vetro di silicato sodo-calcico ad un processo di scambio ionico per conferirgli una maggiore resistenza alle sollecitazioni meccaniche e termiche. Gli ioni di piccolo diametro presenti sulla superficie e sui bordi del vetro sono costituiti da ioni di diametro maggiore; in questo modo la superficie e i bordi della lastra risultano messi in compressione. L’indurimento chimico permette di ottenere compressioni maggiori dell’indurimento termico, ma la profondità dello strato superficiale compresso è molto minore. Le caratteristiche minime (dimensionali, di frammentazione e di resistenza meccanica) sono definite nella norma di prodotto UNI EN 12337-1.
Il valore minimo della resistenza caratteristica a trazione per flessione fb;k delle lastre di vetro presollecitato indurito chimicamente da adottare per le verifiche di resistenza è pari a 150 MPa.
Infine, il vetro indurito, a differenza del vetro temperato, si frattura a partire da un centro di propagazione generando fessure disposte a raggio. I frammenti che si generano sono piuttosto grandi, simili a quelli del vetro ricotto e pertanto tali vetri sono consigliabili per prevenire lo sfilamento dagli appoggi.
I vetri induriti vengono prodotti con spessori fino a 12 mm, in quanto nascono difficoltà di controllo della qualità per spessori superiori.